Warwick Custom Shop Vol.3~Custom Shop Bassができるまで~
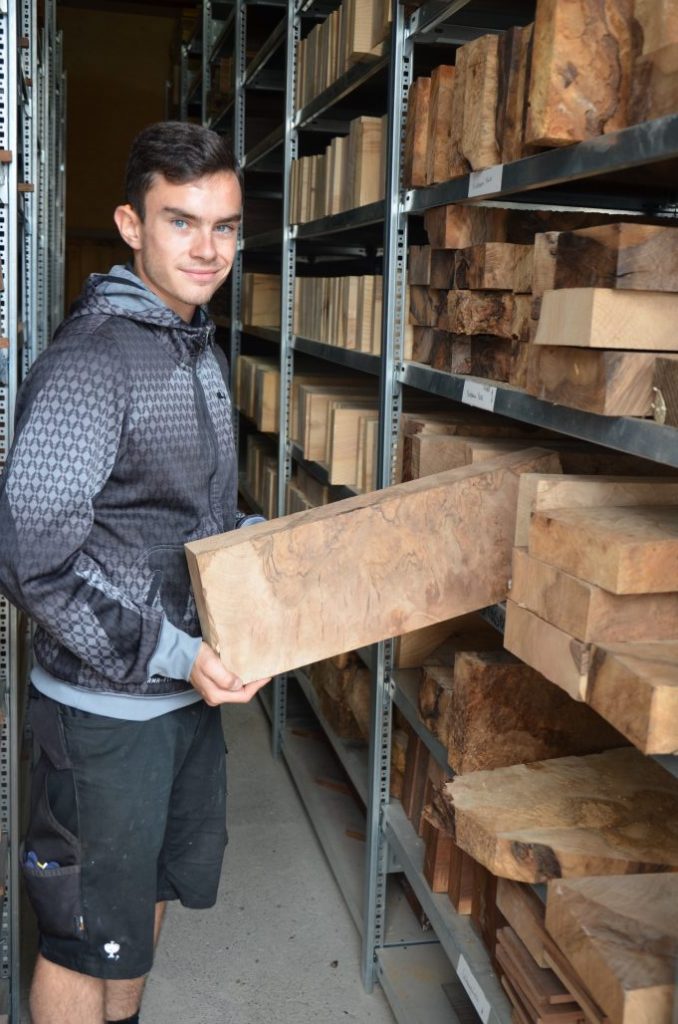
皆さんこんにちは。今月から名古屋に転勤となりましたタク・オカモトです。
これまで同様ベーシストの皆さまの役に立つ情報やここだけの話を日本のド真ん中からから発信していきますので、よろしくお願いいたします!!
さて、前回、前々回、お話しさせて頂きましたWarwickベースですが、今回は昨年Warwick Factoryを訪問した際の写真を交え、製造工程についてご紹介して参ります。
写真かなり多めでお送りいたしますのでぜひともご覧くださいませ。(写真はクリックでより詳細にご覧いただけます。)
~Warwick Custom Shop Bassができるまで~
前々回、Warwickは膨大の量の木材を保有していると紹介しました。
ヨーロッパ最大級の木材を保有するWarwickの貯材庫から改めてご覧いただきましょう!!
こちらです!!ドン!!
Warehouse
左:貯材庫内の風景。写真の3~4倍くらいの木材が積んでありました。
右:丸太で仕入れ、細かく切り分ける前の状態。ちなみに写っている二コラの身長は170cm以上あります。
クレーンがありました笑。高い場所にある材をピックするときにつかうのでしょう。
Custom Shop専用貯材庫
カスタムショップ用の木材は厳選され、↑の専用倉庫で管理されます。
一見小さな倉庫に見えますがそばにポツンとおいてある台車と比べてください・・・5mはあるでしょう。当然ですが奥まで木材はぎっしりです。
Warwick Factry Inside
さてここからは工場内を紹介していきます!!
木材をカットするマシンやBodyを成型するマシーンがずらっと並んだ現代的できれいな工場です。
Body
倉庫にて乾燥された木材は、カットされ木目の近い材ごとに接着されます。
Neck
木材を有効に使用するための工夫。上のネック、フレイムでてますね~。
トラスロッドが仕込まれ、指板接着前の状態。
メイプル材で蓋をしてありますが、そのサイドの2つのくぼみにはネック補強用の鉄製棒が埋め込まれます。
ちょうど12Fからスタートする位置で、ハイ置きを予防しているといえるでしょう。
Fret Machine
なんと、フレットの溝掘りから打ち込み、フレットサイドのカットなど指板周りの加工、塗装はすべてマシーンが行います。最も演奏者の手に触れ、シビアな加工が求められるポイントですが、それを機械がこなしてしまうあたりはさすがドイツという感じでしょうか。ちなみに塗装マシーンは訪問時には稼働していませんでした・・・残念・・・。
Hand Shaping
カスタムショップ製品のみ、職人の手によってもう一ひと手間かけて成型が行われます。
ボディー成型、フレット加工など、多くの場面が機械によって行われるWarwick製品ですが、やはり最終的に人の手が入ることの重要性を感じさせてくれます。
最終調整
木部の加工が完了した個体は配線、最終チェックが行われます。
ドイツ工場で生産されるCustom Shop、Germany Proはもちろん、Rock Bassシリーズもここで最終調整が行われます。
番外編~LED~
カスタムショップ製品はより良質な木材を使用している点も特徴ですが、指板インレイ等にLEDを搭載できるのも特徴です。
偶然LED搭載作業前の指板がありましたのでご紹介いたします。
右にある棒状にLEDの取りつけられたものを指板に埋め込むと左の状態になるということですね。
LEDの内側、私も見るのははじめてでした。
いかがだったでしょうか!?
急ぎ足で紹介してまいりましたが、Warwickがいかに木材を保有し、機械と職人の手によって素晴らしい楽器ができるか、ご覧いただけましたでしょうか。
それでは、また次回おあいしましょう!!